I’ve been NC machining for a while now.
50+ Years
My dad let me run my first NC when I was 10 years old.
A few years later I was running NC’s as a summer job when in high school. I grew up as NC and CNC machining industry grew up. When I started I was the “new kid”. Now I’m the “old timer”.
I’ve witnessed a lot of changes in the industry, and I happy to say that almost all of them were for the better.
Long before CNC was the buzzword it is now. Long before many of today’s seasoned programmers were even born, long before many of our competitors had NC’s, I was programming G-code. I still remember working with JQ, before he joined Orange County Choppers. On the show he was a “CNC Gangsta”. Before that I remember him working on his first Haas toolroom mill.
I first learned G-Code in the early 70’s. My friends who were computer programmers, working with hi-level programming languages thought I was nuts.
I always thought it was the coolest thing; to string a bunch of characters together and make a 30 horsepower machine the size of a truck move to a position within a thousandth of an inch. To me, it was magic, and to tell the truth, after all these years, it still is.
A short history of the CNC

In those days there was no “CNC” (computerized numerical control). It was only NC, meaning there was no computer attached.
Mills and lathes ran from an NC tape. Sometimes paper or, for long runs, we’d punch mylar tape. Tape was 1 inch wide, and for big programs hundreds of feet long, punched full of holes in EIA format. One wrong character, one misplaced hole, on sloppy keystroke, and you had to start over.
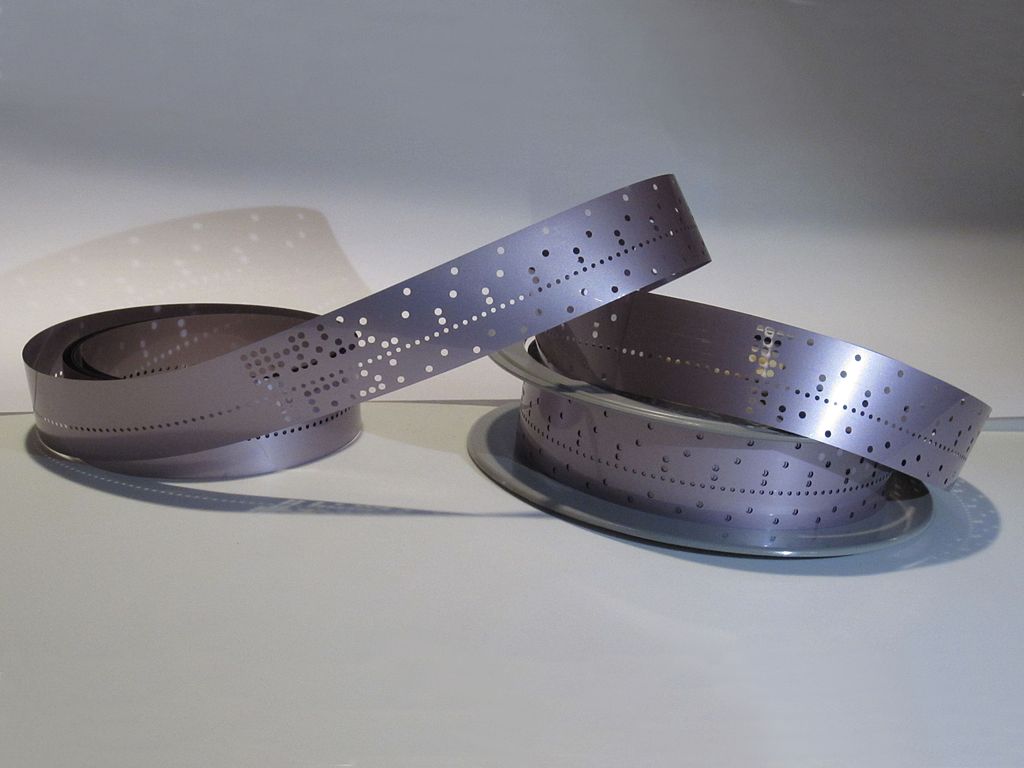
Eventually our machines got CNC retrofits, and you did have a computer (albeit fairly primitive) and then you could write and edit right there on the machine. I still remember the rush of my first edit on the control, something we now take for granted.
CNC’s evolved, they got better, smarter, faster. Fanuc came along and made G-code very standardized and very stable.
And then CAM (computer aided manufacturing) software came to the machining world. APT and Compact II programming was available, and the world of machining changed again.
Those were all million dollar mainframes no one could afford, so we did time-sharing, and were charged by the minute.
Then the personal PC came along, and we could have CAM software right on our own computer. STC went through 5 different programming software systems before settling with Mastercam in 1988. We’ve been using Mastercam consistently for over 30 years.
CAM got better and better, dynamic tool paths meant you could now scream through parts that ten years you had to crawl through. Parametric macros made menial tasks quick, leaving the hard work to the controls. Probing meant you could verify dimension right on the machine without needing to bring it to inspection, further streamlining production.
And as for tools, well, cutter innovation seems to evolve so quickly, it seems I’m testing out new endmills on a monthly basis.
Innovate or Stagnate
Yeah, there’ve been a lot of changes in metal cutting industry through the years.
Many shops I’ve known just wouldn’t or couldn’t keep up with all those changes. Too expensive. Too hard. Too new.
For me, each new change has made it a little easier, a little faster, a little better, more streamlined and a little cooler. So you could focus on making that part that’s just a little harder than you could before; able to push capabilities a little further..
Paul Mutzek, Lead CNC Programmer